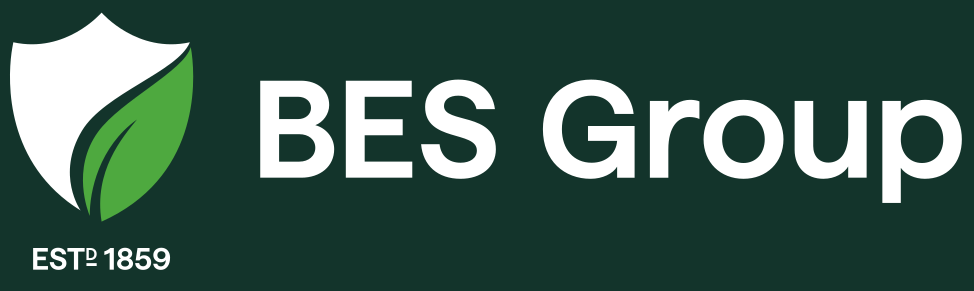
Reduce risk and maintain compliance with our specialist risk management services.
We’re proud to be a leading provider of complete life cycle risk management solutions. From ensuring asset safety and legal compliance with our thorough engineering inspections to driving operational efficiency with our specialist non-destructive testing services, (and much more in between), we’re proud of the long-lasting partnerships we have formed with our customers over the last 160 years, based on the value of our solutions.
Sector
Manufacturing
Location
United Kingdom
Services
Remote Monitoring and Data Services
Oil Analysis
Vibration Analysis
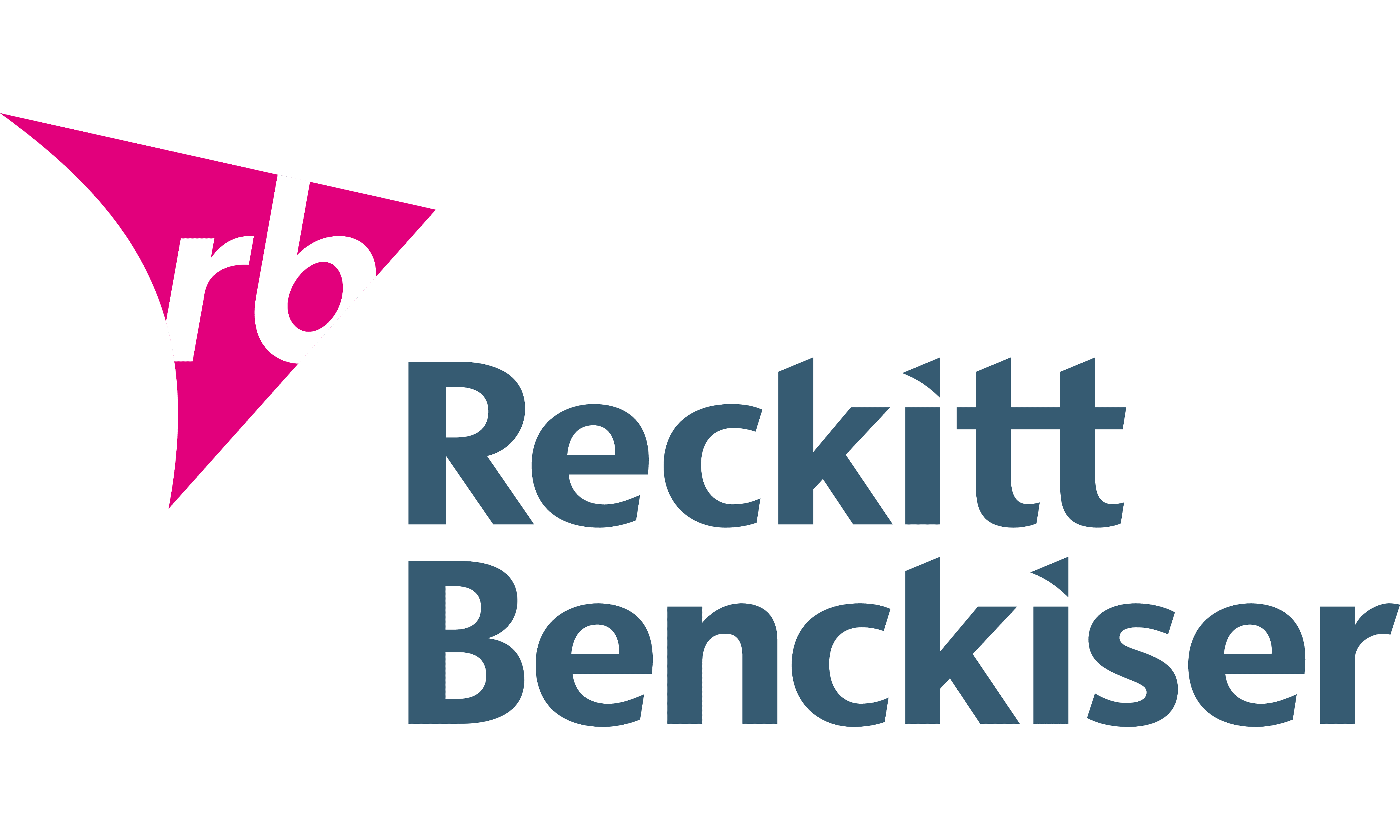
Our partnership with Reckitt Benckiser
Overview
Vibration data collected from a hydraulic pump motor showed an increase in vibration amplitudes on the motor’s DE bearing, indicating deterioration of a coupling insert.
Site engineers removed the hydraulic pump motor during planned downtime and found the coupling spider badly worn. The coupling was replaced, saving an estimated £3,712 in unplanned downtime cost avoidance.
We provide ongoing vibration testing and oil analysis for a multinational consumer goods company based in the UK. As part of our service, data is collected from multiple moulding machines on a bi-monthly basis.
The challenge
The solution
Our reliability engineers provided vibration and Stresswave analysis on the machines to track the health of the assets.
Data was collected from the extruder motor and gearbox, as well as the hydraulic pump motor. Oil samples were taken from the gearboxes and the hydraulic system hammers for signs of wear and free movement.
The result
Vibration data collected in December 2019 on machine 1 (hydraulic pump motor) showed an increase in vibration amplitudes on the motor’s DE bearing. Analysis of the data showed raised levels of synchronous activity with a dominant two times running speed peak – see figure 1.
Figure 1: Showing the increase in vibration on the motor DE bearing.
Due to the motor being mounted upon the tank by means of a spigot, misalignment was ruled out and the most likely cause was identified as deterioration of a coupling insert. Although the vibration amplitudes were not excessive, due to the criticality and time between site visits, it was recommended that further investigation should be carried out on the motor’s coupling insert.
Site engineers removed the hydraulic motor off machine 1 during planned downtime and found the coupling spider badly worn. The coupling was replaced. Data collected off the asset in February 2020 shows vibration levels had returned to historical levels – see figure 2.
Figure 2: Showing the decrease in vibration on the motor DE bearing
Most FMCG production facilities are driven by the requirement for maximum availability and reliability during operation. By identifying this fault, the cost avoidance of planning and execution of maintenance activities to unexpectedly resolve was estimated at £3,713.00.
Key outcomes
Replaced coupling during planned downtime.
Vibration levels returned to historical levels.
Saved an estimated £3,712 in unplanned downtime cost avoidance.
Contact us to find out more about Vibration Analysis, Remote Monitoring and Data Services and Products.
Related Case Studies
View All Case Studies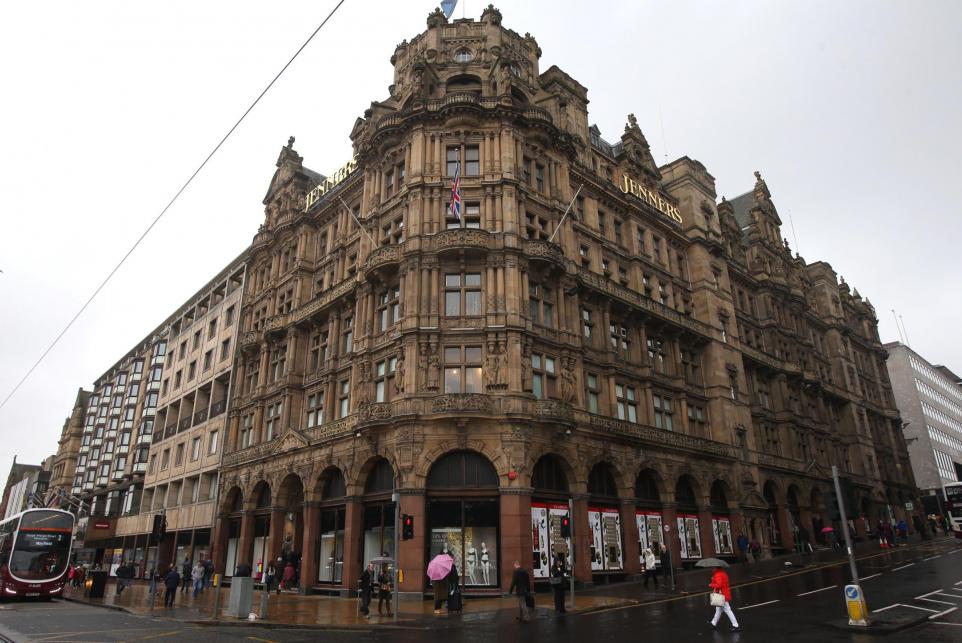
Preserving History and Ensuring Safety with Structural Monitoring During The Jenners Building Re-development
Read more.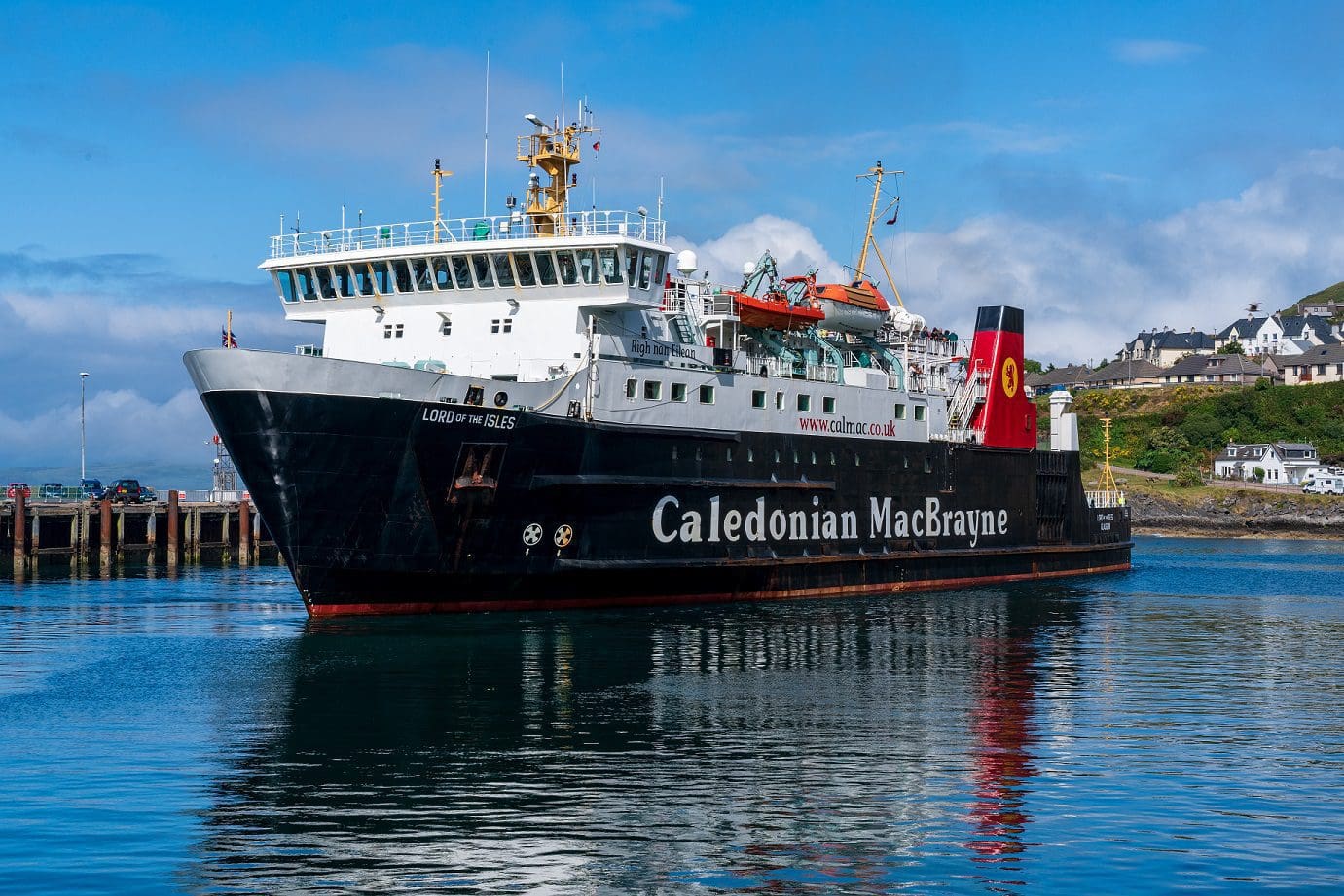
Vessel Downtime Avoided for UK Ferries Operator
Read more.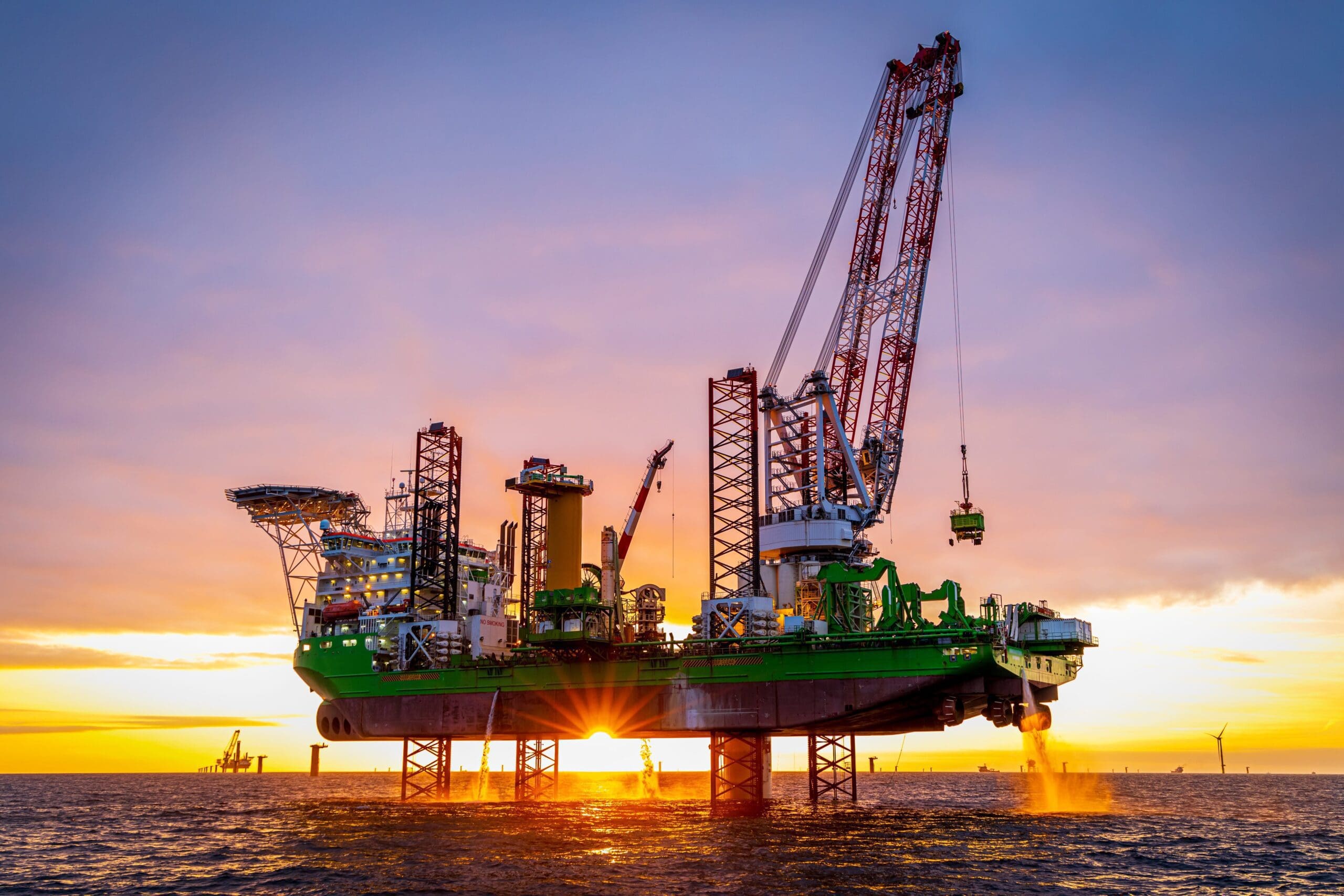