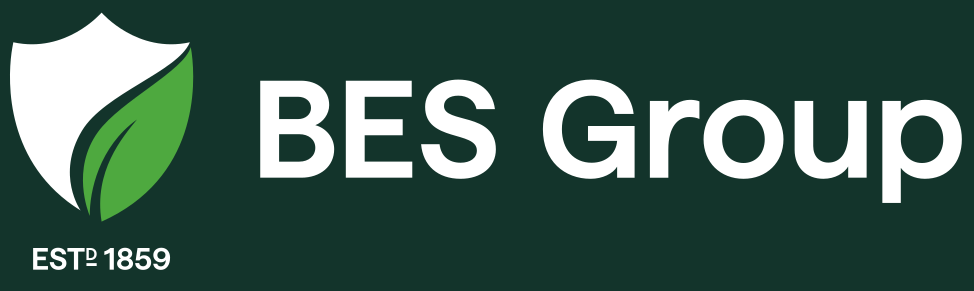
Reduce risk and maintain compliance with our specialist risk management services.
We’re proud to be a leading provider of complete life cycle risk management solutions. From ensuring asset safety and legal compliance with our thorough engineering inspections to driving operational efficiency with our specialist non-destructive testing services, (and much more in between), we’re proud of the long-lasting partnerships we have formed with our customers over the last 160 years, based on the value of our solutions.
Sector
Fasteners, Manufacturing
Location
West Midlands
Services
Fastener Testing
Metallurgical Testing
Critical fastener testing services for hazardous material transport
Project overview
Some of our clients require more rigorous laboratory testing than others. In one case, precision was critical as we participated in a high-profile project involving the transportation of hazardous materials for the nuclear industry.
Our testing laboratory was tasked with carrying out precise testing on bolts, specially manufactured to secure the lids of containers used for transporting irradiated nuclear fuel by rail. The importance of ensuring the reliability and safety of these bolts was of utmost importance, given the critical nature of the materials being transported.
The project also involved collaboration among several key stakeholders, including:
- Our laboratory
- A UK-based fastener manufacturer
- Government entities overseeing nuclear safety
- External inspection bodies monitoring the project
The Challenge
Our involvement in the project began during its initial planning stages. We underwent a comprehensive assessment to demonstrate our testing capabilities and our commitment to delivering high-quality, accurate testing services. We understood the importance of maintaining compliance standards for this essential safety item, and we were dedicated to meeting and exceeding them.
The manufacturing of the flask lid bolts was a vital stage of this project to ensure safety. Failure of the bolts could potentially lead to fatal consequences, severe injuries, and significant environmental damage for an extended period.
Precise testing and accurate results were crucial.
To aid with the production process, we carried out meticulous testing on the bolts supplied by the manufacturer, to ensure they were made from the right material and were suitable for exposure to harsh conditions.
Through our dedication to safety, we were able to provide accurate outcomes and guarantee the reliability of the flask lid bolts. This ensured the overall safety of the project and minimised the potential for accidents, injuries, and environmental harm.
The Solution
To provide deliver the very best testing services for this project, we expanded our accreditation and implemented new methods within our laboratory to ensure compliance with all relevant regulations. We are now the sole UKAS test laboratory in the UK authorized to conduct these specific tests.
This expansion of our accreditation not only showcases our dedication to quality but also highlights our commitment to maintaining the highest standards in testing services.
Our skilled technologists conducted various tests to verify the bolts’ performance in challenging conditions, detect any material defects or flaws during production, and evaluate the impact of the heat treatment stage on material quality. Our comprehensive tests included:
- Macro examination
- Grain flow analysis
- Micro examination
- Hardness testing
- Tensile testing following the Irradiated Fuel Transport Specification
The Results
During the 18-month project duration, our team maintained a close collaboration with all stakeholders involved to ensure the successful development of the product, and transportation of critical fuel. This involved a series of crucial steps and interactions:
- Regular communication with the customer: We engaged in frequent discussions and feedback sessions with the customer to align our progress with their expectations and requirements.
- Interaction with inspectors: Inspectors were involved throughout the process to review the product’s development stages, ensuring compliance with regulations and standards.
- Engagement with end users: Understanding the needs and preferences of end users was key. We gathered feedback from them to refine the product and enhance its usability.
By actively involving these key parties in the project, we were able to uphold the highest standards of quality and safety, meeting the stringent requirements essential for the application while prioritizing public and environmental safety.
What our partners on this project have to say:
“For me to make ten or 12 visits to the laboratory on this project, and to have no cause for complaint, is a record not many outfits have achieved over my 20-odd years in this position. I look forward to my next visit to Rotech whenever that may be. Keep up the good work and high standards.”
External Inspection Body Representative
“BES Group has provided consistent quality, and exceptional technical support and advice throughout the project. We are very appreciative of their services.”
Project End-User
Key Outcomes
Enhanced safety
assurance and reliability for transporting hazardous materials
Accreditation expansion
of laboratory capabilities to support testing requirements
Collaboration
with high-profile stakeholders, manufacturers, and government entities
Related services
Fastener Testing
Metallography
Hardness Testing
Tensile Testing
Contact us today
Related Case Studies
View All Case Studies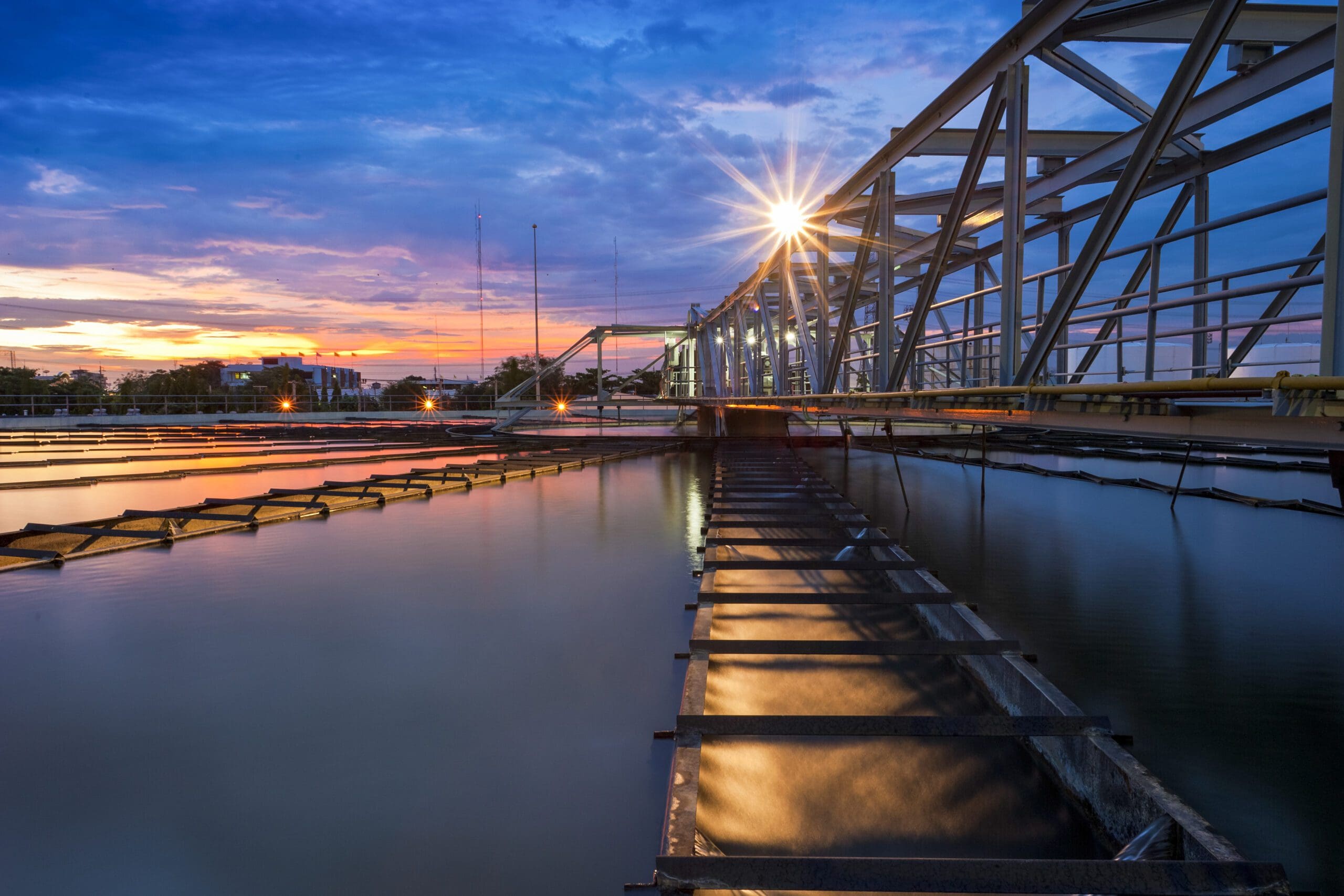
Keeping Wessex Water Running Smoothly
Read more.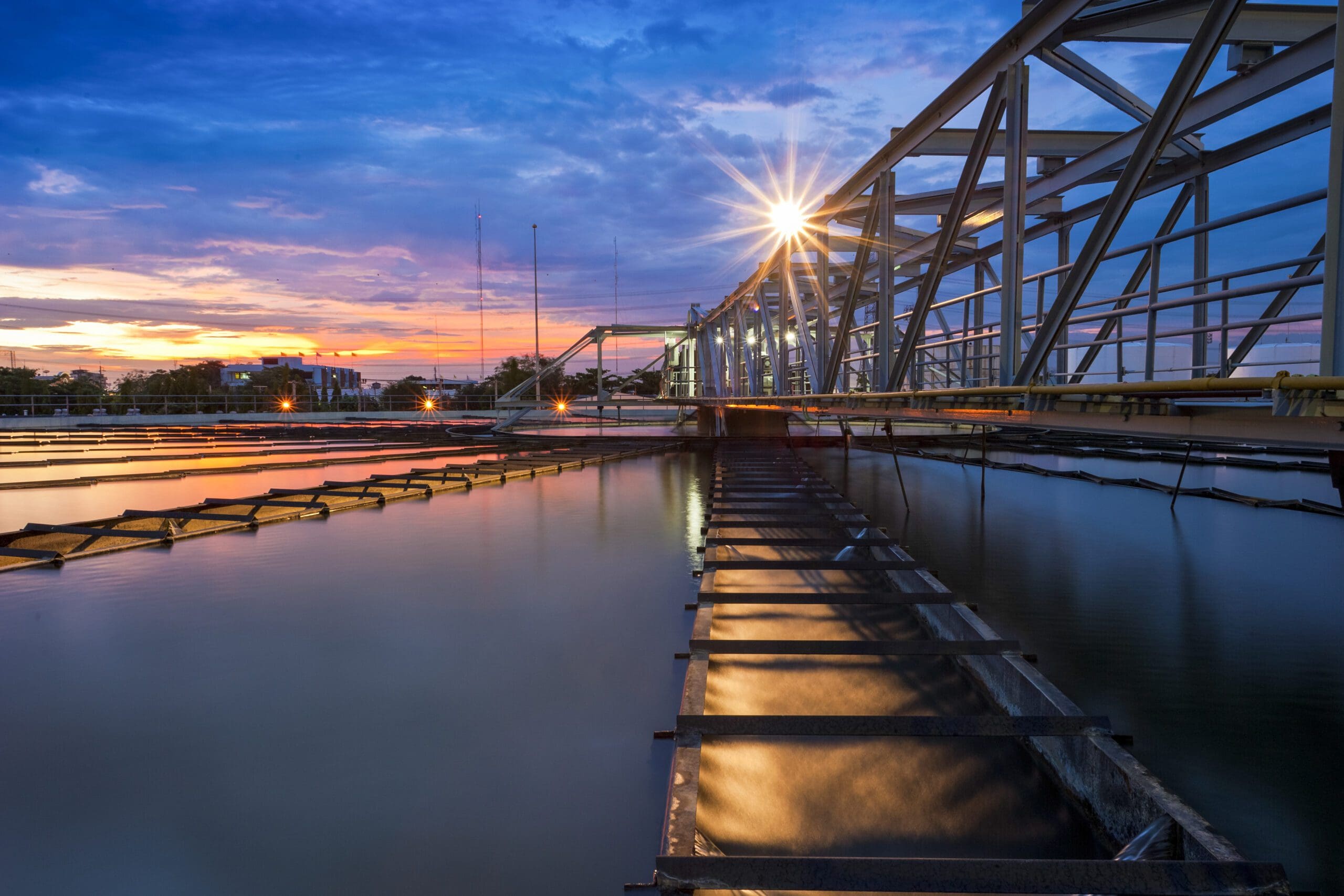
An innovative solution for Thames Water
Read more.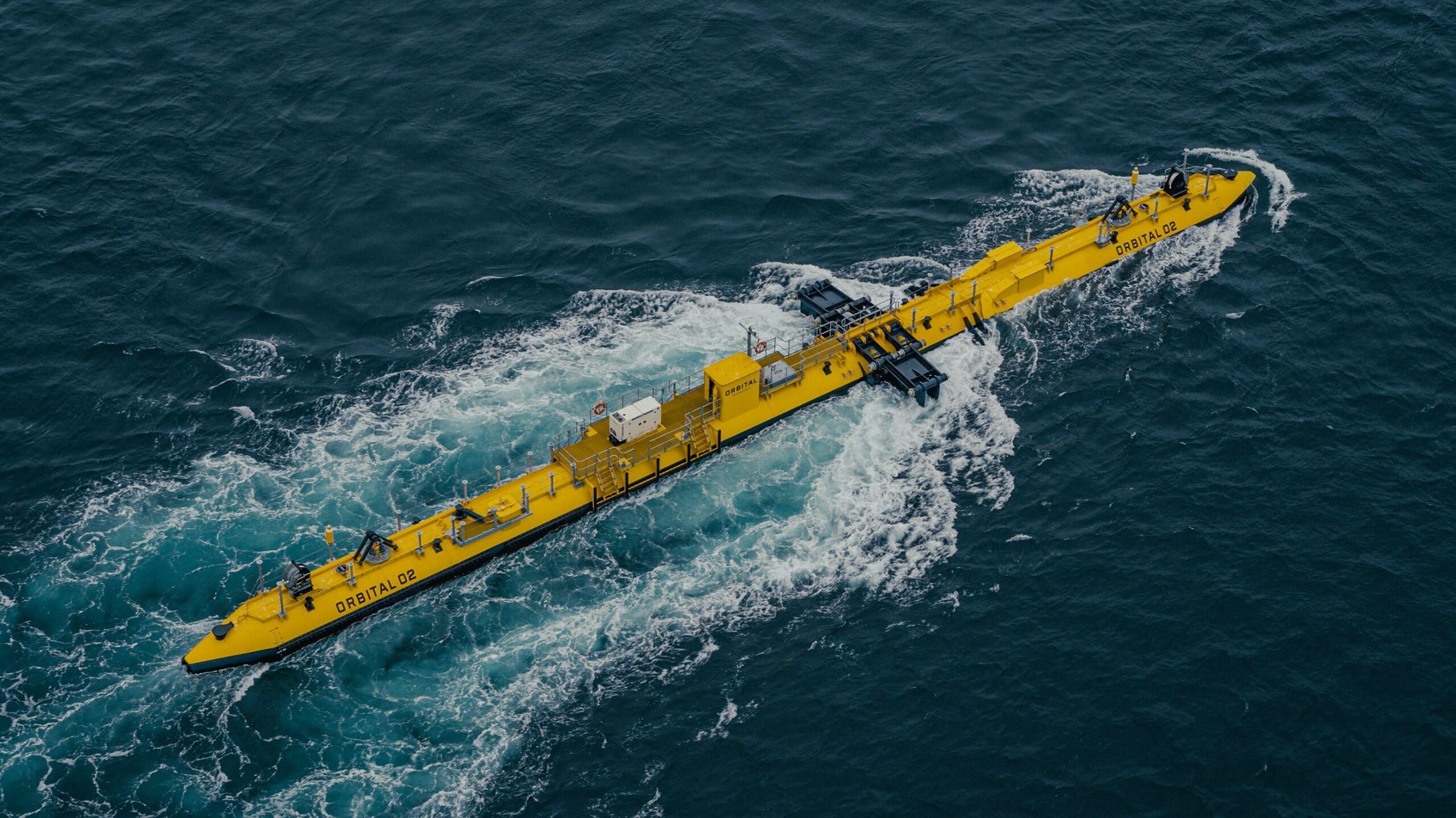