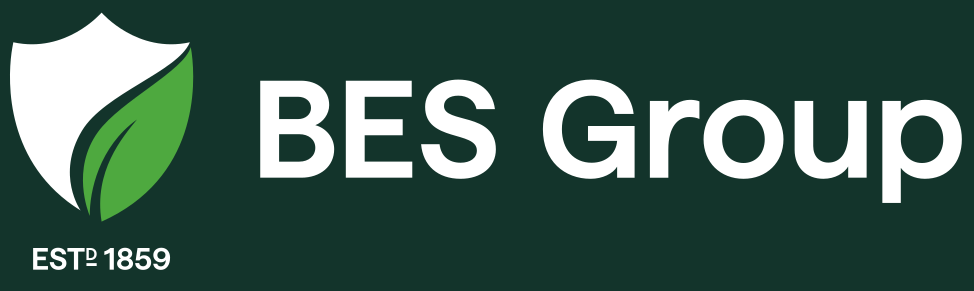
Reduce risk and maintain compliance with our specialist risk management services.
We’re proud to be a leading provider of complete life cycle risk management solutions. From ensuring asset safety and legal compliance with our thorough engineering inspections to driving operational efficiency with our specialist non-destructive testing services, (and much more in between), we’re proud of the long-lasting partnerships we have formed with our customers over the last 160 years, based on the value of our solutions.
Sector
Rail
Location
United Kingdom
Services
Oil Analysis
Remote Monitoring and Data Analysis
Our partnership with Alstom Chester
Overview
A rail client identified a solid deposit on the fire switch of a 175 engine. The mechanical switch was providing false pressure readings due to the button sticking.
Further investigation discovered that the liquid inside a fire bottle was leaching through into the switch, causing metallic components of the switch (i.e. copper and zinc) to corrode and fuse with other components of the switch.
The challenge
A solid deposit was discovered on a fire switch which was mounted to the cooler raft of a 175 engine on the operator’s diesel multiple unit passenger trains.
The mechanical switch was providing false pressure readings due to the button sticking; a potentially critical fault that required urgent investigation.
The solution
The result
The SEM topography outlined the elemental composition of the black deposit to be mainly organic matter (carbon and oxygen) and brass (copper and zinc).
Upon further investigation, the contents of the fire bottle were determined to be TRIDOL S 6% AFFF, which contains diethylene glycol monobutyl ether. This is thought to be the likely source of the carbon and oxygen.
The liquid inside the fire bottle was believed to be leaching through into the switch, which when interacting with moisture in the air caused the metallic components of the switch (i.e., copper and zinc) to corrode and fuse with other components of the switch.
The rail transport company worked with the supplier of the fire bottles to identify a switch to eradicate the issue and installed the new switch on every engine across their fleet.
Critical downtime was avoided, and the operator is now one of our largest customers and has implemented a managed oil analysis programme as part of their maintenance strategy.
Key outcomes
New switch installed.
Managed oil analysis program implemented.
Critical downtime avoided.
Contact us to find out more about Oil Analysis, Thermography Surveys and Remote Monitoring and Data Services.
Related Case Studies
View All Case Studies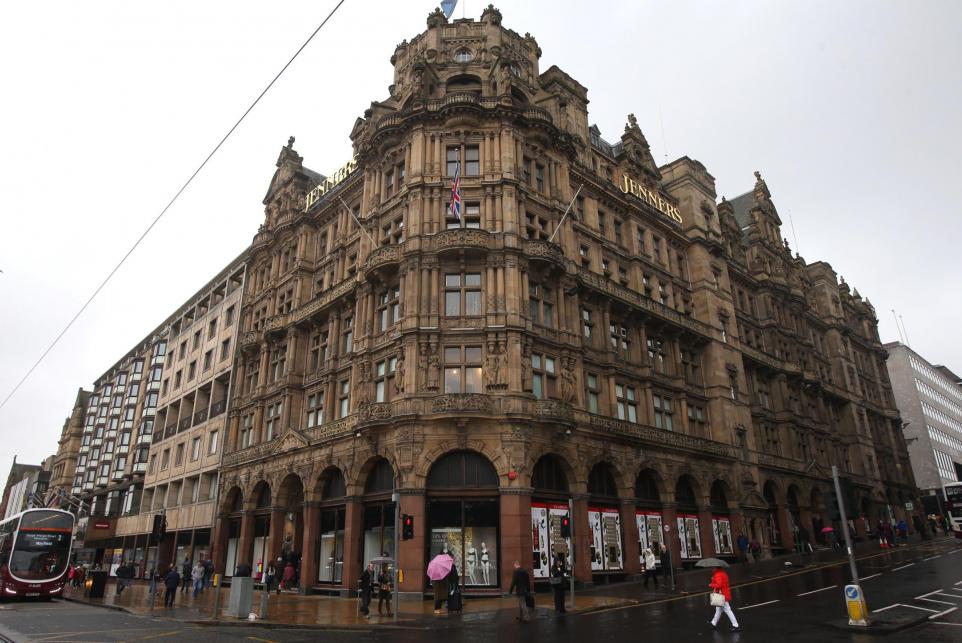
Preserving History and Ensuring Safety with Structural Monitoring During The Jenners Building Re-development
Read more.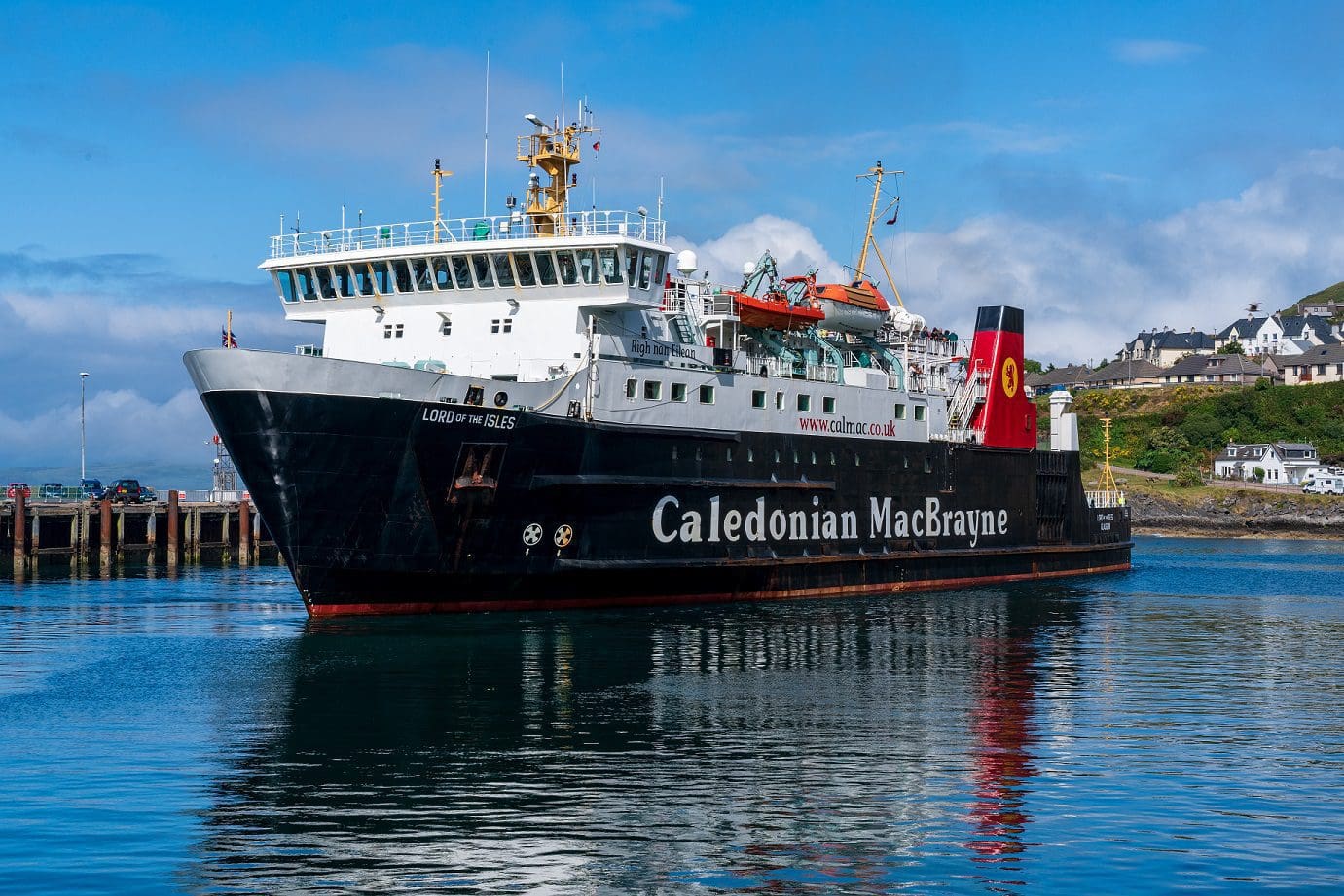
Vessel Downtime Avoided for UK Ferries Operator
Read more.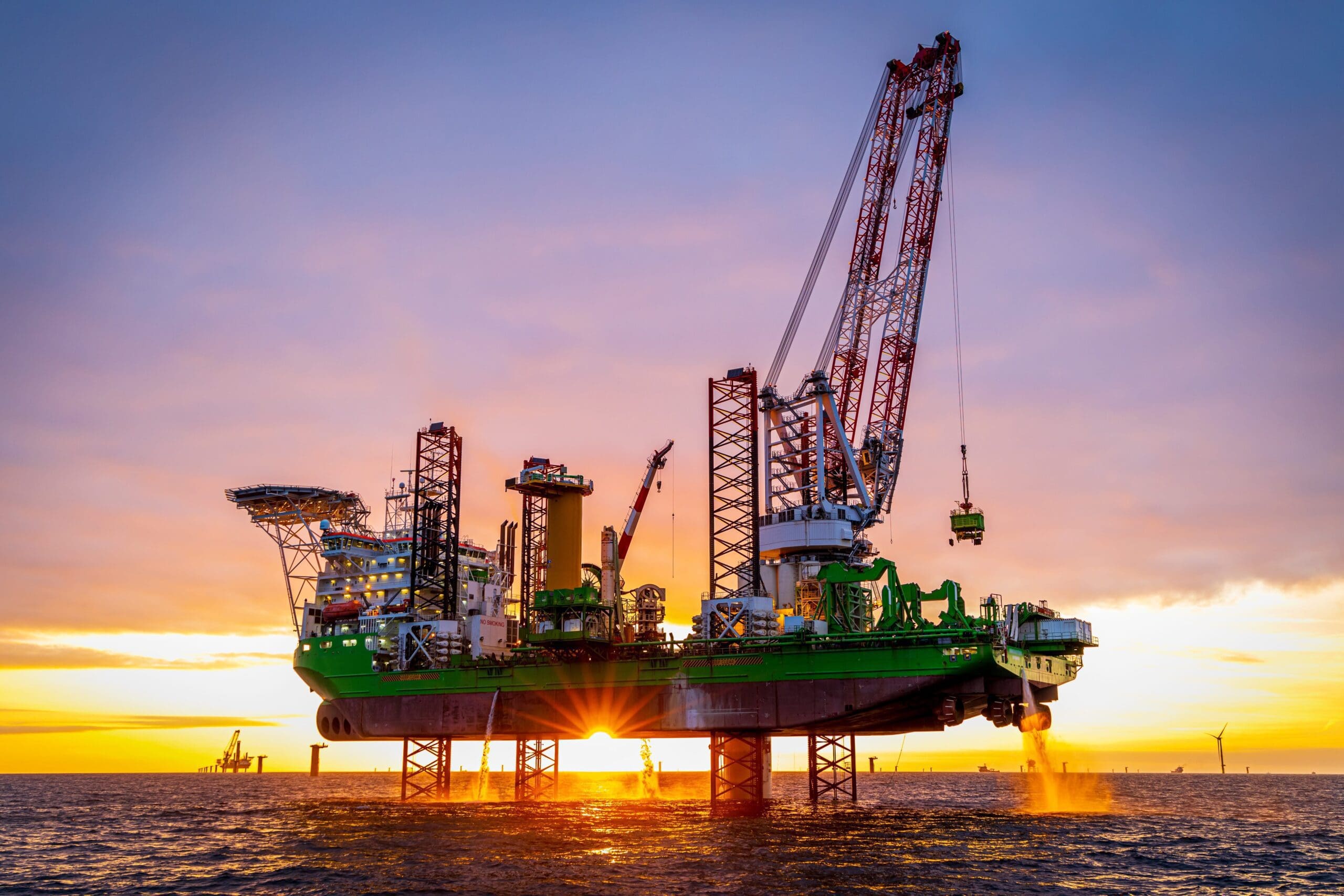